Deep Learning for Design
Real-time, design-sensitive CAE postprocessing for all?
Reporting results is the second most pleasant activity for CAE Engineers.
The most pleasant one is achieving design optimization.
What if we could do all of that in real-time?
Thanks to the power of Deep Learning and the Neural Concept approach, Product designers can feed a software with arbitrary CAD shapes and get 3D Engineering predictions (surrogates of CAE: CFD, stress & thermal etc.) as quasi-real-time output, even on an everyday laptop. The data-driven approach yields the type of output that engineers need without the burden of the mesher and solver.
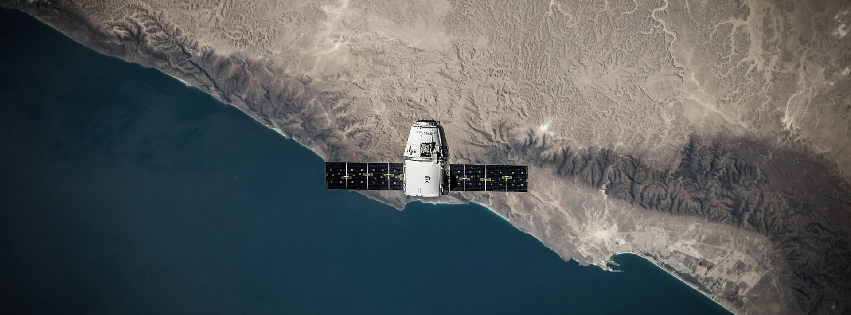
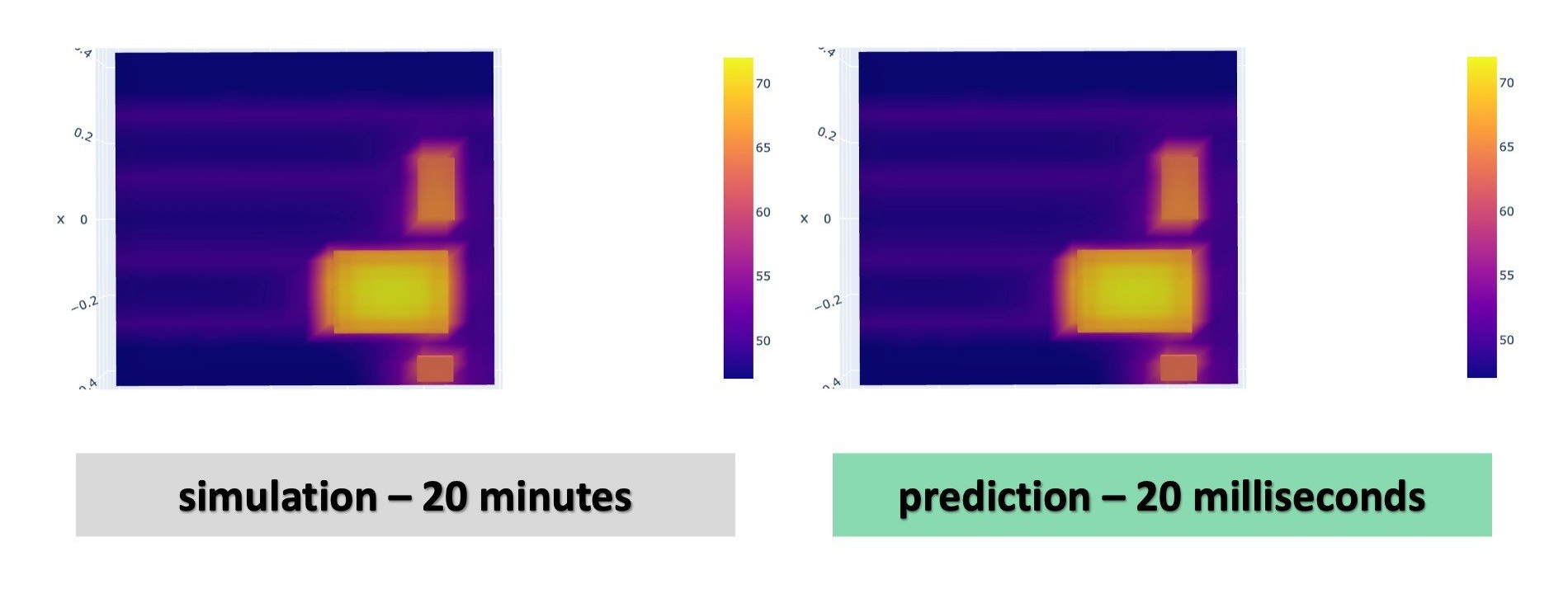
Let us start with a specific application case (you can extend the usage of Deep Learning to any CAE: CFD, FEA, Electromagnetics...).
I will focus on thermal analysis, namely an electronics cooling case for aerospace, namely the onboard electronics (chips on a cold plate) on a satellite (see above figures).
As Engineering prediction outputs, in general from you can get:
- global numbers (e.g. the max or average temperature),
- local 3D fields (a temperature field as shown here),
- global or local signals (e.g. an evolving average temperature during a transient).
In the above figure, you can see a visual comparison between High-Fidelity physics-driven simulation (left) and Deep Learning data-driven prediction. High-Fidelity physics-driven simulation takes 20 minutes Deep Learning data-driven prediction takes 20 milliseconds!
The final users can rely on plug-and-play usage and, within an App or some CAD-embedded solution, users can create shapes and get their desired outputs on the go.
Behind this friendly usage, there is an underlying data-driven approach that requires, as the word says, a database to feed a Deep Learning neural network. The underlying "data science project" is part of training and testing the Deep Learning neural network. and can be carried out by consultants, or data science experts within your company.
Courtesy ESA BIC Zurich, we can expose the Deep Learning elements for this specific project here and in a downloadable white paper.
The picture shows the main results from the Deep Learning project:

Beyond "making a single simulation faster": Design Space Exploration on your fingertips.
The importance of the Deep Learning approach goes far beyond "predicting in fractions of a millisecond". The implications for product design can be:
- Real-time Design Space Exploration. Some of our users are starting to explore 100'000 designs and more per days for design space exploration and generative design.
- Real-time Performance Maps. Other users are interested in performance maps and understanding how a performance map changes with design changes.
- Real-time Interactive Design. Other users are embedding Deep Learning into CAD. Imagine a company with a High-Fidelity CAE simulation group. As high-fidelity, think of whatever primary commercial or opensource code in CFD, thermal, FEA and electromagnetics) and CAD Designers who cannot or would not use High-Fidelity CAE.
On the last point 3., I do not agree on separating high fidelity CAE and designers' CAE, leading to double standards within organizations.
In the past, reasons for this "divorce" were:
- High fidelity CAE is too complicated.
- There are not enough licenses.
- It can be lengthy if you have no HPC
In 2021, it would be much better to exploit available technology and to have a data-driven solution for CAD designers based on high-fidelity data. Therefore, we propose plug-and-play a trained surrogate model into CAD or a company Intranet. The design engineers will not need to do any training since they already know what to do - design their products. The prediction part is one button push time's away.
Two keywords explain how this tool is technically serious:
- uncertainty prediction (see also some advanced research work here, including Neural Concept staff) and
- transfer learning.
To close, Transfer Learning.
Transfer learning is another ingredient that facilitates an even larger return on investment from Deep Learning: the initial neural network time/effort is reduced by orders of magnitude when the case is just giving new High Fidelity simulations.
Imagine your focus on aerodynamics moves from luxury cars to new projects on SUVs and do some preliminary high fidelity CFD. The aerospace of SUVs (CFD and maybe even experimental data) will complete the Deep Learning model's initial training based on the aerodynamics of luxury cars. The effort for SUVs will be a fraction of the initial attempt for luxury cars aerodynamics.
In conclusion, there are several open roads. Industry leaders have tested and adopted the Deep Learning solution, and any of the above three implications should be a call to action for other organizations.